Kapittel 2
Referanseanlegg for avfallsforbrenning med CO2-fangst
Kapittel 2
For å kunne vurdere hvilke CO2-fangstteknologier som egner seg til avfallsforbrenning er det etablert et referanseanlegg «KAN Referansa» som gjenspeiler avfallsforbrenningsanleggene i KAN gruppen. På forenklet måte vises i figuren nedenfor hovedkretsløpet for avfall, energi og røykgass (som inneholder CO2-en). Et typisk avfallsforbrenningsanlegg har et fjernvarmenett tilknyttet og produserer strøm med dampturbin. Røykgassen renses til å tilfredsstille utslippskrav og slippes deretter ut til atmosfæren. Både avfallforbrenning (i blått) og fjernvarme/strøm (i rødt) er hensyntatt.
«KAN Referansa» har en kapasitet på 100.000 tonn avfall per år og driftes 8000 timer per år. Med en målsetning om å fange 90 % CO2 blir dermed også mengde CO2 som må sendes til lagring 100.000 tonn per år.
Avfallsforbrenningen produserer damp ved 40 barg og 400 °C med en total varmeproduksjon på 275 GWh, noe som med en typisk mottrykksturbin gir 50 GWh i strømproduksjon per år hvorav 10 GWh brukes internt til forbrenning. Etter turbin blir mesteparten av varmen (175 GWh) brukt i et fjernvarmenett som har et årlig behov på 200 GWh og må derfor ha en spisslast på 25 GWh. Resten av varmen må kjøles bort på sommertiden når behovet i fjernvarmenett er lavt.
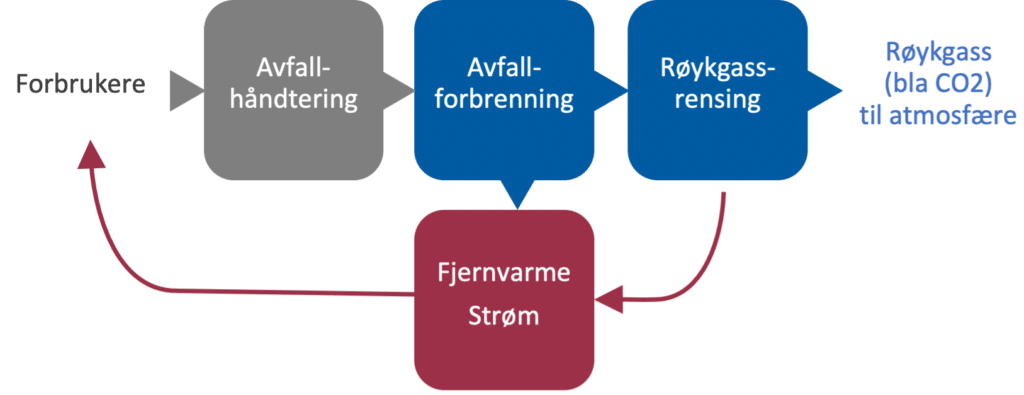
2 Kretsløpet for avfallsforbrenning med CO2-fangst
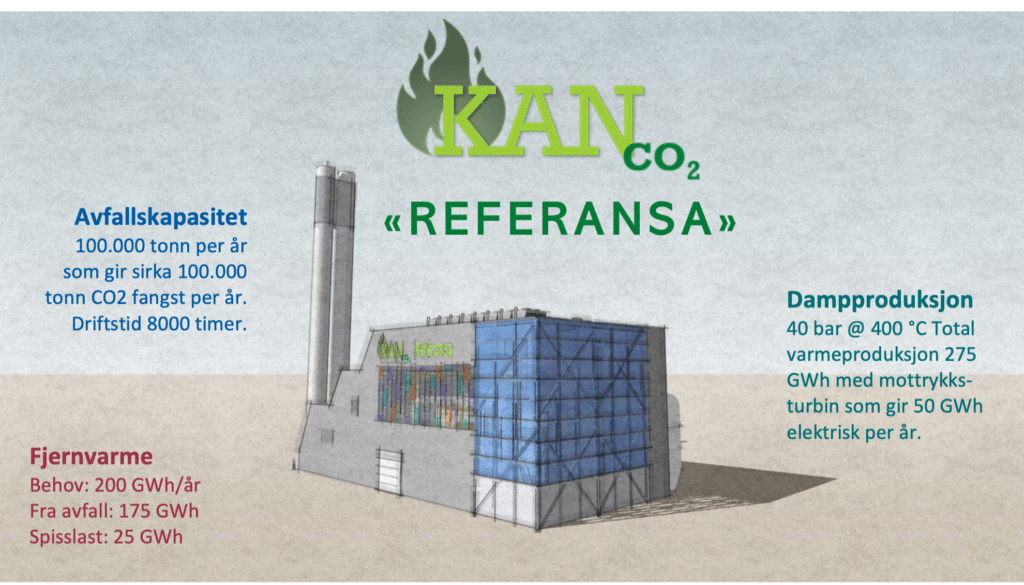
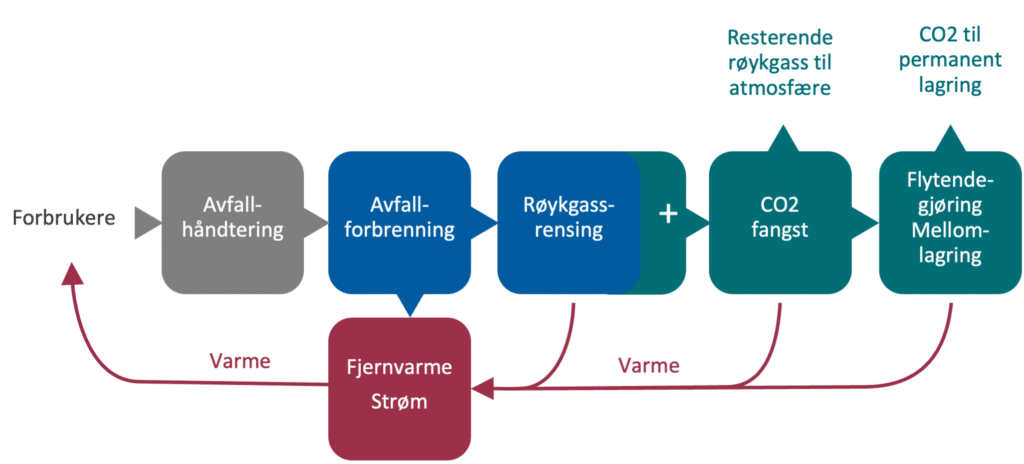
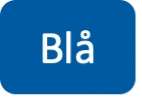
Blå representerer eksisterende anlegget (avfallsforbrenning med røykgassrensing) uten karbonfangst og lagring.
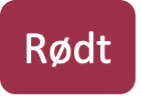
Rødt representerer fjernvarme/damp med strømproduksjon.
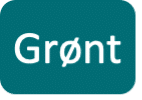
Grønt representerer fangstanlegget hvor del-prosessen med en liten plus-symbol er «forbehandling» kan omfatte både deler av eksisterende røykgassrensing og nye rensetrinn nødvendig for å kunne fange CO2 i røykgassen fra avfallsforbrenningen og mellomlagre denne flytende på lokalt CO2-lager.
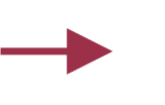
Pilene fra anleggene til fjernvarmen representerer «hjelpesystemer/integrasjoner/etc. og omhandler tiltak i grensesnittene mellom avfallsforbrenning, fjernvarme, fangstanlegg, øvrig energiforsyning m.m. Transport av fanget CO2 er nærmere beskrevet i kapittelet «Transport og mellomlager» på side 79.
2.1 Typer energiproduksjon
Avfallsforbrenningsanlegg kan gjenvinne varmen fra forbrenningen av avfall på ulike måter. Dette er vist i tabellen nedenfor. Varmen gjenvinnes i de fleste tilfeller til varme til fjernvarmenettet og/eller elektrisk til strømproduksjon. Enkelte anlegg med flere forbrenningslinjer kan komme til å ha en kombinasjon av de ulike alternativene i tabellen. Hetvannsanlegg vil gi noe større fjernvarme-leveranse.
Anleggsdesign | Energiproduksjon | Konsekvens for karbonfangst |
---|---|---|
Kun hetvann | Ingen strømproduksjon og kun fjernvarme | Damp er ikke tilgjengelig til karbonfangst og hvis teknologien krever dette må dampen lages separat |
Damp med mottrykksturbin og kjøling direkte mot fjernvarme | 15-20% av energien konverteres til strøm og 85-80% til fjernvarme, mulighet for bypass av turbin. Overskudd av fjernvarme kjøles bort. | Damp kan brukes og kan hentes på fire måter: – Damp tas oppstrøms turbin, dette er relativt enkelt men reduserer strømproduksjon. – Hvis turbin er tilrettelagt kan dampen tas fra et mellomsteg i turbin, noe som gir best virkningsgrad og litt mindre tap i strømproduksjon. -Damp tas oppstrøms turbin og ekspanderes gjennom ny mottrykksturbin tilpasset fangstanleggets behov. -Damp kjøres gjennom eksisterende turbin og trykkes opp igjen med dampvifte. |
Damp med kondenserende turbin | 15-25% av tilgjengelig energi konverteres til elkraft i totrinns turbin, avtapping til fjernvarme på mellomtrinnet, vakuumkondenser med kjøling. |
2.2 Fjernvarme, referanse
Avfallsforbrenningsanleggene er knyttet til lokale fjernvarmesystemer med ulik størrelse og ulike sesongvariasjoner. Hvor stor andel levert effekt og energi av fjernvarmen som kommer fra avfallsanlegget vil variere fra sted til sted og over tid. Eierskap og kontroll over fjernvarmen varierer også fra lokasjon til lokasjon. Samtidig representerer koblingen mellom avfallsforbrenning og lokal fjernvarme en nøkkelfaktor for smarte integrasjoner ved introduksjon av et karbonfangstanlegg. Temperaturforhold på fjernvarme tur og retur spiller også inn på mulighetene for integrasjoner.
Basert på kjente varighetskurver for ulike fjernvarmeanlegg er det etablert et referanse-fjernvarmenettverk. Nøkkeltall for dette fjernvarmenettverket er som følger:
- Behov i fjernvarmenettet: 200 GWh (75 MW peak)
- Tilgjengelig avfallsvarme: 175 GWh (88% av levert varme i fjernvarmen)
- Spisslast fra alternativ kilde: 25 GWh (12% av levert varme i fjernvarmen)
- Timer med avfallsvarme på maks effekt: opp til 3000 timer per år.
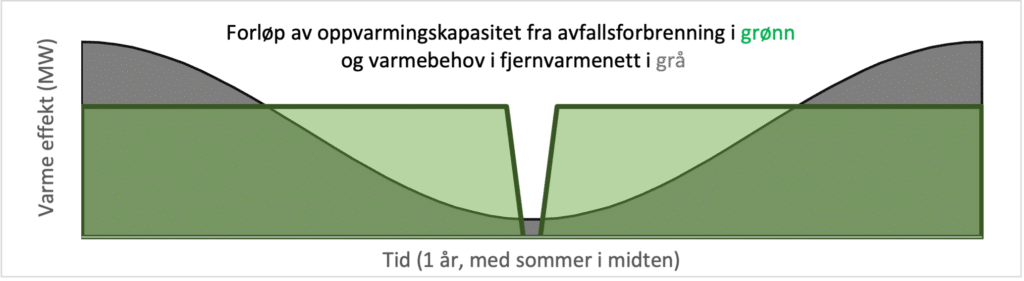
fra januar til desember.
Varighetsdiagram for «KAN Referansa» uten karbonfangstanlegg
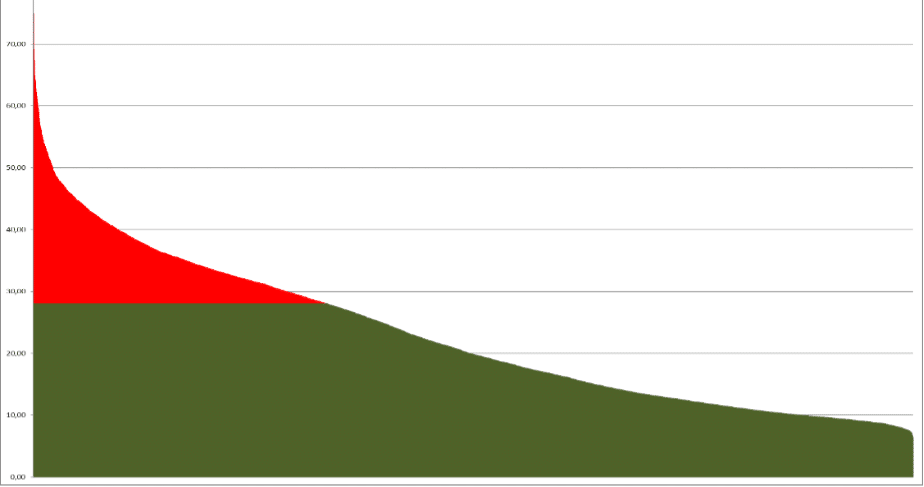
Effektutnyttelse mot fjernvarme
I motsetning til rene kraftverk og rene industriprosesser er norske avfallsforbrenningsanlegg i stor grad grunnlast i fjernvarmeanlegg hvor «lasten» har store sesongvariasjoner. Avfalls-forbrenningslinjene har derfor lengre perioder med «overskuddsvarme» som helt eller delvis kan dekke opp for energibehovet til et karbonfangstanlegg.
Dagens største forbrenningsanlegg i Norge har stor variasjon i hvor lenge anlegget har full effektutnyttelse mot fjernvarmenett. Denne tiden kan variere fra 5 % av året til over 40 % av året og des lavere dette tallet, des høyere potensialet er for at CO2-fangst kan benytte denne varmen. Jo høyere tallet, jo mer effekt et fangstanlegg vil måtte ta varme som tidligere var brukt i fjernvarmenett.
Energiutnyttelse
De største avfallsforbrenningsanlegg i Norge varierer mellom 65 % og 95 % total energiutnyttelse. Jo høyere tallet, jo mer av varmen som kjøles bort fordi den ikke kan brukes i fjernvarmenettet.
Anlegg med lav energiutnyttelse vil ha flere timer hvor leveranse av varme til et CO2-fangstanlegg ikke vil påvirke fjernvarmeleveransene negativt. Økt behov for ekstra spisslast eller behov for smarte integrasjoner vil være lavere for anlegg med lav energiutnyttelse.
2.3 Forbrenningsteknologier
De to mest vanlige forbrenningsteknologiene i forbrenningsanlegg er ristforbrenningen og forbrenningen med CFB (Circulating fluidized bed).
Den viktigste forskjellen mellom disse er miljøytelsen og -utslipp. CFB har typisk lavere NOx- og SOx-utslipp sammenlignet med ristforbrenning, noe som blant annet gjør det enklere å imøtekomme kravene til røykgass-sammensetning for et CO2-fangstanlegg.
I Norge er ristfyring mest utbredt og det er to anlegg som benytter annen teknologi. Haraldrud benytter CFB, mens Averøy benytter gassifisering.
Referanseanlegget er basert på ristfyring.
2.4 Røykgassrensing, referanse for røykgassrensingen
Konfigurasjon røykgassrensing og røykgassammensetning
På tross av at avfallsforbrenningene har samme utslippskravene å forholde seg til, kan røykgassen variere mye fra anlegg til anlegg. Lokasjon og alder på anlegget påvirker disse forhold. Røykgasstemperatur i skorstein varierer fra 60 °C til 140 °C og røykgassammensetning kan også variere vesentlig, selv om de er under grenseverdier.
Hvorfor er dette viktig?
Det er viktig å gjøre en grundig kartlegging av røykgassammensetningen ved ulike driftsforhold. Ulike komponenter i røykgassen kan påvirke degraderingsraten til amin-solventer og legge føringer for materialvalg i fangstanlegget for å hindre korrosjon. Det kan også være behov for å gjøre oppgraderinger eller sette inn nye rensetrinn i røykgassrensesystemet for å møte kravene til røykgassammensetning fra et fangstanlegg. Dersom disse forholdene ikke blir hensyntatt i designet vil det medføre risiko for økte drifts-/vedlikeholdskostnader og nedetid på anlegget.
En kan anta at det vil være både nødvendig og tilstrekkelig å oppgradere eksisterende anlegg til Best Available Technology (BAT) krav for 2023.
I referanseprosessen skal all røykgass kjøles fra 120 °C til maks 55 °C.
Referanse for røykgassrensing defineres på følgende måte: «Røykgassrenseanlegget har en konfigurasjon og nødvendige rensetrinn slik at det kun er behov for nedkjøling og prekondisjonering (SOx) av røykgass i en DCC før absorber. DCC og ny røykgassvifte for å overkomme trykkfall på gassiden inngår i leveransen til leverandør av fangstanlegget.»
2.5 Karbonfangstanlegget
Standard beskrivelse av fangstanlegget
Et standard MEA (30wt%) aminanlegg er den typen CO2-fangstanlegg som er benyttet som referanseanlegg på CO2-fangst. Herunder dekkes uttakspunkt nær eksisterende skorstein til utløpt av kjøler nedstrøms CO2-stripper. Anlegget er dimensjonert for å fange 90 % av CO2 i røykgassen med en årskapasitet på 100 000 tonn CO2.
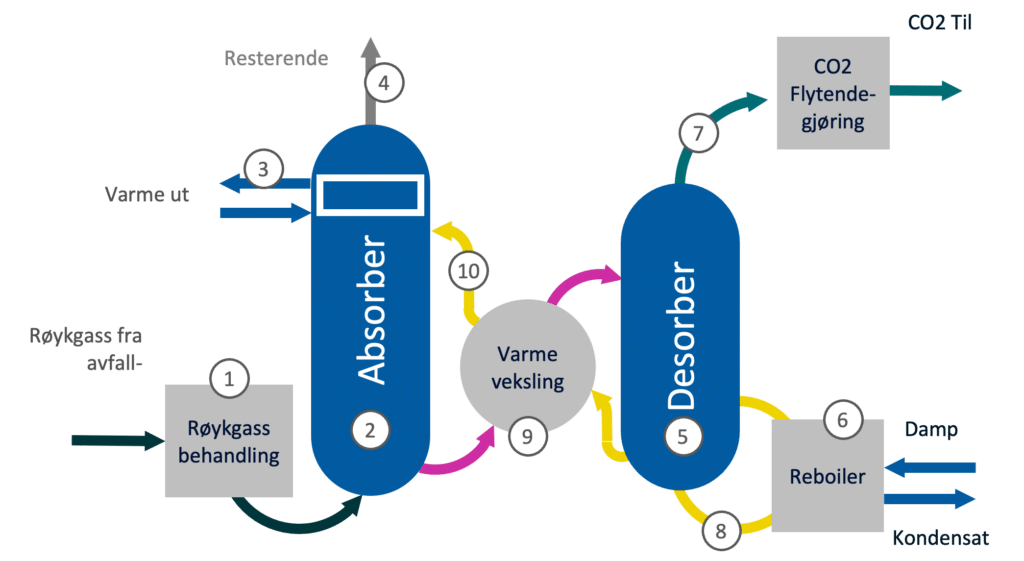
(1) Direct contact cooler (DCC)
Før røykgassen føres inn på absorber i fangstanlegget går den gjennom en direct contact cooler (DCC). Formålet med DCCen er todelt:
(a) kjøle ned gassen til et temperaturnivå hvor absorbsjon av CO2 er mest effektiv (typisk rundt 40-55 °C for amin)
(b) Vaske bort korrosive komponenter som SO2, mv ved tilsetning av lut.
Røykgassen kjøles ned under sitt opprinnelige duggpunkt og vil man også få utkondensering av vann i DCC. Denne vannstrømmen må transporteres til et eget vannrenseanlegg for behandling og deponering av avfallsstoffer. Røykgassen som forlater DCC-en vil være på duggpunktet. Nedstrøms kanaler og vifte må være i korrosjonsbestandige materialer.
(2) Absorber
I absorberen bindes CO2 i røykgassen til solventløsningen gjennom en kjemisk reaksjon. For amin-solventer avgir reaksjonen varme slik at man får en temperaturgratient over absorberen. Siden absorbsjonsevnen til amin er best ved lave temperaturer avtar effektiviteten etter hvert som temperaturen stiger gjennom absorberen. Typisk er temperaturen på røykgass/amin 60 °C når den entrer vasketrinnet (6) på toppen av absorberen.
Stor kontaktflate mellom gass og solvent er avgjørende for å sikre effektivt absorbsjon. For å øke kontaktflaten fylles en seksjon kolonnevolumet med pakkingmateriale. Pakkingen vil være en motstand som genererer mer trykkfall. Dette må kompenseres ved dimensjonering av røykgassviften oppstrøms fangstanlegget. Solvent uten CO2 tilsettes i øvre del av absorberen, mens solvent mettet med CO2 pumpes ut fra bunnen.
(3) Absorber water wash section
Når temperatur stiger vil vann og amin fordampe. For å hindre amin-utslipp over tillatte grense-verdier, og redusere vanntapet fra fangstanlegget, installeres en eller to vannvaskeseksjoner i øvre del av absorberen. Vannvaskeren kjøler ned og kondenserer fordampet vann/amin. I tillegg installeres en dråpefanger som effektivt fanger små dråper.
(4) Absorber stack eller retur til eksisterende skorstein
Etter vannvasken går renset røykgass ut av absorberen. Avhengig av lokale forhold og utslippskrav må røykgass ettervarmes for å sikre tilstrekkelig spredning ved utslipp. Ettervarming må i mange tilfeller gjøres ved hjelp av en varmekilde i avfallsforbrenningsanlegget. Røykgassen kan også føres tilbake til skorstein til avfallsforbrenning. Vurdering av dette må gjøres per situasjon/lokasjon.
(5) Desorber/stripper
Etter at CO2 er absorbert pumpes solvent med CO2 til desorber/stripper kolonne. Solventen tilsettes i øvre del av kolonnen. I desorberen varmes løsningen opp til typisk 120 °C (for amin) og CO2 drives ut av solventen. På tilsvarende måte som i absorberen er stor kontaktflate mellom gassfase og væskefase med nødvendig for å sikre effektiv stripping av CO2. En seksjon av kolonnevolumet er derfor fylt med pakkingmateriale for å øke kontaktflaten. Desorberen er trykksatt (typisk 1 barg) og trykket bidrar til å kompensere for trykkfall over pakkingseksjonen. CO2 og vanndamp forlater toppen av desorberen.
(6) Reboiler
Varme for å drive CO2 ut solvent-løsningen tilføres i en reboiler. Solventløsningen tilføres i et kokende væskebad på skallside og kokeprosessen driver av CO2 og vanndamp. Typisk benyttes mettet lavtrykksdamp (damptrykk ca. 2 barg) på rørsiden av reboiler, men hettvann og hetolje kan også benyttes.
Typisk spesifikt varmebehov for denne MEA-prosessen med standard prosesskonfigurasjon er 3,6 MJ/kg CO2, som tilsvarer 1 MWh/tonn CO2 fanget.
(7) Overhead stripper condenser
CO2 og vanndamp går ut på toppen av desorberen og holder her en temperatur på typisk 110 °C. Gassen kjøles ned til ca. 30 °C før den går til anlegget for komprimering, kondisjonering, tørking, flytendegjøring. Ved nedkjøling i overhead stripper condenser vil en stor andel av vanndampen kondensere. Vann og CO2 i gassfase separeres i en kondensattank, hvor CO2-gass mettet med vanndamp går til CO2-kompressorene, og kondensert vann pumpes tilbake til desorberen.
(8) Reclaimer
Over tid vil de fleste solventer degraderes som følge av kontakt med urenheter i røykgassen. For å fjerne degraderingsproduktene inkluderes normalt en regeneringsprosess (reclaiming). Regenering gjøres etter behov og hyppigheten vil avhenge av mengden og type urenheter som er i røykgassen.
Degraderingsraten avhenger av type solvent og mange av de proprietære aminene som er utviklet av teknologileverandører hevdes å ha svært lav degraderingsrate.
(9) Cross heat exchanger
Siden absorber og desorber har ulike driftstemperatur settes det inn en kryssvarmeveksler hvor varmt solvent uten CO2 (typisk 120 °C) varmeveksles mot kald solvent med CO2 (typisk 50-60 °C). På denne måten spares energi til kjøling og oppvarming av solvent i hhv. absorber og desorber.
(10) Lean amine cooler
Etter kryssvarmeveksleren har solvent uten CO2 fremdeles litt høy temperatur Derfor kjøles solventen ytterligere i en egen varmeveksler før den går inn på absorberen.
CO2 compression and Liquifaction
Etter OH Stripper Condenser (7) ledes strippet CO2 til et anlegg for kompresjon og flytendegjøring. Kompresjon er energikrevende og utløser et kjølebehov.
Gitt referanseanlegget blir det termiske energibehovet til stripper ved full drift antatt til å være 12,5 MW og 100 GWh per år.
2.6 Capture as a service
Enkelte av leverandørene tilbyr ulike varianter av fangst som en tjeneste. Det er gitt indikasjoner om at kostnaden for en slik tjenester kan være ned mot 1100-1300 kr/tonn CO2. Av dette utgjør kostnader for slutt¬lager mellom 400-600 kr/tonn. Hva som vil inngå i en slik tjeneste er uklart, men det vil trolig forutsette at tjenestetilbyderen får levert klargjort tomt, og tilgang på nødvendig varme, kjøling og andre hjelpesystemer som er nødvendig for drift av anlegget.
Et prosjekt driftet som «capture as a service» vil etter Norsk Energi sin vurdering måtte planlegges og utføres som om det var gjennomført uten slik «driftstjeneste». Om leverandøren skal levere fangst¬tjenesten inklusiv egen energiforsyning er det stor fare for at man velger mer kostbare løsninger siden muligheten for smarte integrasjoner vil være mer utilgjengelig.
Gitt at tjenesteleverandør må ta økt risiko ved å tilby fangst som en tjeneste må man forvente at det også er et risikotillegg i prisen.
2.7 Investeringskostnad (Capex)
Etablering av en benchmark for investeringskostnad (capex) for et ettermontert karbonfangstanlegg er krevende. En capex-estimat vil være beheftet med ulik usikkerhet ved ulike modenhetsnivåer.
Prosjektets capex vil i stor grad styres av oppdragsgivers kvalitetskrav. Et stedbygget spesialtilpasset fangstanlegg med god plass for tilkomst og eget prosessbygg vil ha høyere capex enn en standardisert modulløsning basert på kontainere og prefabrikerte løsninger. Derimot kan et spesialtilpasset anlegg være mer kostnadseffektivt når anlegget er stort (flere hundre tusen tonn CO2 per år).
Designkrav og funksjonskrav i prosjektets design basis forventes derfor å ha stor innvirkning på endelig capex for prosjektet. Selve CO2-fangstanlegget forventes også bare å utgjøre en mindre andel av total capex hvor faktorer som tomtekjøp, bygg og grunn, kjølevannsanlegg, kompresjon, flytendegjøring og mellomlager også inngår som vesentlige kostnadsfaktorer.
I en synteserapport fra svenske Energiforsk (Eliasson m. fl. (2021)) foreslås følgende forenklede formel for beregning av investeringskostnad for et CO2-fangstanlegg, inklusiv kompresjon. Det er antatt at denne formelen ikke inkluderer lokale lagertanker, tomtekostnader og grunnarbeider.
[1000 EURO] = 15520 x tonn per time CO2^ 0,6339
[1000 EURO] = 15520 x 12,5^ 0,6339 = 77 MEUR
For referanseanlegget gir denne formelen en total forventet capex på 77 MEUR antatt uten grunnarbeider.
En av KAN partnere, BIR, har gjennom mulighetsstudier og annet forarbeid estimert at et anlegg med en kapasitet til å fange 100.000 tonn per år fra avfallsforbrenning i Bergen må ha et investerings-budsjett på ca. 1 milliard norske kroner. Dette bekrefter at formelen gir et bra første estimat, gitt at formelen er kun for selve fangstanlegget uten prosjektspesifikke kostnader.