Chapter 4
Transport and intermediate storage
Celsio CCS, Returkraft Langemyr, Statkraft HVS and Borg CO2 have all conducted studies of transport and intermediate storage of CO2. These studies have been reviewed and the solutions in the studies have been evaluated and compared. Based on this, a generic, scalable design of transport and intermediate storage has been developed. This design has been used in the preparation of rough indications of the cost of transport assignments and intermediate storage facilities.
Restriction
In this context, transport and intermediate storage includes installations and operations with the following interfaces: Export flange from buffer storage at capture facilities and import flange on cargo ships. This interface is well adapted to a value chain that uses transport by truck.
Transport av CO2
The solutions that have been evaluated in studies carried out previously are transport in the liquid phase on the truck, transport in the liquid phase on trains and transport in the liquid or gas phase in pipelines. A compilation of these conclusions has been prepared, and liquid-phase transport by truck comes out on top. Long-term costs are higher, but they have higher feasibility and significantly lower project risk.
Mellomlagring av flytende CO2
A model has been developed to make cost estimates of a generic and scalable tanker park for intermediate storage of liquid CO2. The model is based on cost estimates from the studies reviewed. The estimates can therefore, under given assumptions, be considered to have a relatively high accuracy (± 30%), but they have significant limitations in the form that major cost drivers such as ground works, geographical location, property, etc. are not included. The model is also greatly simplified. The costs from the model can be regarded as an indication, but project organizations must check assumptions and delivery limits against the model assumptions.
Methodology
Results documented in the studies in the substrate, including cost estimates, have been used in the preparation of a generic, scalable design. No separate cost estimates have been made at this time. The CO2 capture value chain is relatively new and there is therefore not much comparative material. Therefore, factors for scaling or other adaptation of the design have been developed based on experience from projects with tank facilities for LPG, atmospheric tanks and LNG. The distribution of costs per discipline, factors for proportional reduction in cost and development in cost as a function of asset size are qualitatively assessed based on experience from projects in industry.
Viktig å ta med når en skal vurdere transport og mellomlager av CO2
I denne håndboken kan en finne indiksjoner på kostnader knyttet til transport og mellomlager, herunder kostnader tilknyttet CCS-anlegg med kapasiteter fra 100 000- 200 000 tonn CO2 årlig med en tenkt beliggenhet fra mellomlager 10-20 km unna CCS-anlegget. Kostnader som geografisk plassering, eiendom, grunnarbeider, kai-anlegg, infrastruktur som vei, vann, avløp etc. er ikke med her, men viktig å avklare tidlig.
Celsio CCS
A transport study for the carbon capture project in Oslo was conducted in 2017. It was concluded that truck transport was best suited, and prices were collected for this. Pipeline transport, drilling to Ryen and an existing tunnel from there to the port of Oslo was the best alternative, but the project abandoned this solution for the following reasons:
- High project risk - Extensive and complex government work contributed to high project risk. The development of new regulation plans was considered challenging because of expected public skepticism about the pipeline.
- Time schedule - It was considered likely that the pipeline would not be ready until the capture facilities and downstream infrastructure were in place and ready for operation. Cargo and truck transport had to be used temporarily. And the liquefaction plant would have to be moved from KEA to the Port of Oslo after a period of time.
- Support schemes - The project would only receive support for the operation of the pipeline for 10 years. Operating costs after this would have to be covered by the facility owner.
Estimates have been prepared for EPC costs, including intermediate storage in the Port of Oslo. The scope of the EPC contract was all installations above ground, all disciplines. Four tanks of 1350 m3 were considered sufficient, with a planned port call from Northern Lights every four days. This gives a total volume of 5400 m3 and approximately 1000 m3 in operating reserve. The estimates from the CCS project at Klemetsrud have (together with estimates from other studies) been used as a basis for the preparation of a scalable model for intermediate storage.
Returkraft Langemyr
A transport study conducted in 2021 looked at the transport of liquid CO2 by car, train, or pipeline, as well as gas-phased transport in pipelines. The study included a SWOT analysis where the different transportation solutions were evaluated and given a weighted score. The study concluded that transporting liquid CO2 by truck to Strømsvika is the best alternative, closely followed by transport of liquid CO2 by train to the Brevik terminal. Pipeline transport, both for liquid and gaseous CO2, was not competitive. Investment costs were higher (substantially compared to rail transport), but more decisive – government work was assumed to be very complicated and neighbor/third party interest was assumed to lead to much conflict.
A port study conducted by Norconsult on behalf of Kristiansand Havn KF looked at five different locations for the establishment of a CO2 terminal. The study included preparation of the port area with dock, reception of CO2, intermediate storage and loading to ships. The study examined two alternatives, one where CO2 is transported to the terminal by pipeline (gas phase) and one for truck transport. The establishment of a CO2 terminal in Marvika was recommended, and it is this alternative for which costs are estimated.
- Establishment of dock construction: 54,3 MNOK
- This includes facilitation of the rear area, including blasting, quay construction, engineering and site follow-up, rigging and operation.
- Liquefaction plant: 100.1 MNOK
- CO2 storage tanks: 45.3 MNOK
- 6x500 m3 reclining cylindrical tanks, vacuum insulated.
Statkraft Varme
Statkraft CCS's Pre-feasibility study looked at transport by truck and transport by pipeline, from Heimdal District Heating Plant (HVS) to Orkanger for intermediate storage. From Orkanger, CO2 will be transported offshore to Northern Lights.
The study concluded that trucking pays off due to economic conditions. The pipeline for transport of gas to Orkanger has initially been estimated at approximately NOK 1.2 billion and has not been considered a viable solution.
Statkraft's study assumes exports from intermediate storage every four days. With a one-day port call reserve, the storage volume in Orkanger will be 3300 tons of m3.
The port study is based on the establishment of a new dock at Orkanger where the actual establishment costs of the dock are not included (assumed to be covered by the port owner) and that Statkraft advocates leasing of space and use of the harbor;
Intermediate storage (Capex): The estimate is based on two studies and includes CO2 tanks, pumps, unloading stations and loading arms for boats; estimated cost 184 MNOK including re-serve and cost of ownership.
Intermediate storage (Opex): this is based on initial costs from the Port of Trondheim. Estimated cost 10 MNOK/year.
Borg CO2
In 2021, BORG CO2 conducted a feasibility study for CCS where transport and intermediate storage are described. The study concludes that transport in pipelines will only be relevant for volumes far larger than the 50,000 tons/year assessed. The investment costs for pipeline will be too high. Transport by truck was considered the best solution.
In the Borg CO2 Feasibility Study there is an estimated investment cost for intermediate storage facilities with capacity for storage of 2500 m3, 5000 m3, 7500 m3 and 10 000 m3. The estimates have been prepared by HSE. The cost estimates do not include structural works or installation.
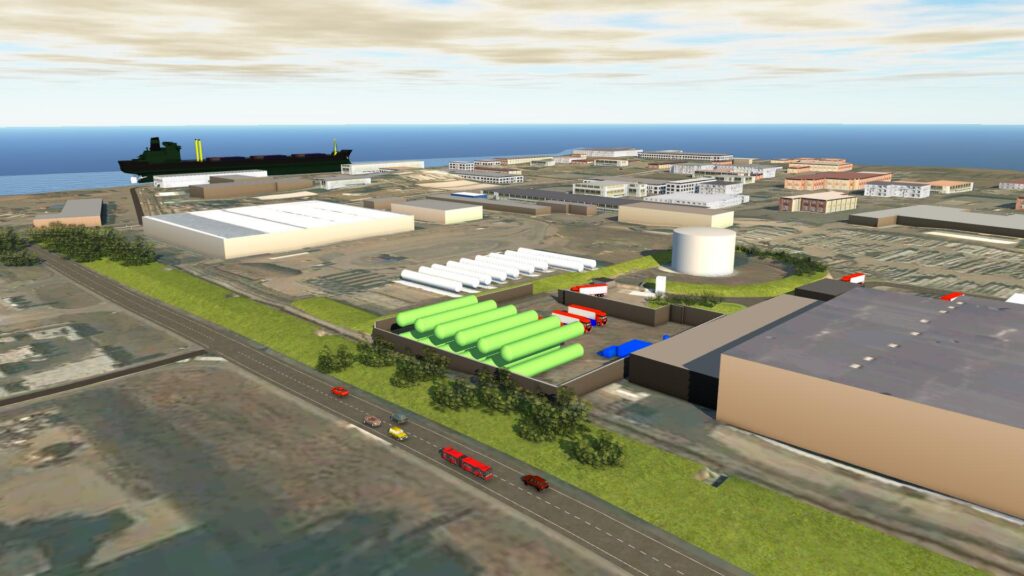
Compilation
Transport by truck has been considered the best method of transport in all studies, even though the price per ton of CO2 per km and costs over time are in many cases higher. Project risk is far lower, and feasibility is higher. Nevertheless, transport in pipelines, either in gas or liquid phase, should be further considered in some cases:
- Proximity to the sea and the possibility of a subsea pipeline reduce project risk in the form of reduced risk of conflict with third parties and less complicated authority processes.
- High volume. No break even has been identified at this time, but the volume should be significantly higher than 400,000 tons/year since project risk was considered too high related to Oslo CCS.
Transport by pipeline will also reduce/eliminate the need for intermediate storage at the capture site and save area as there will be no need for facilities for unloading to cars. This will provide cost and area savings.
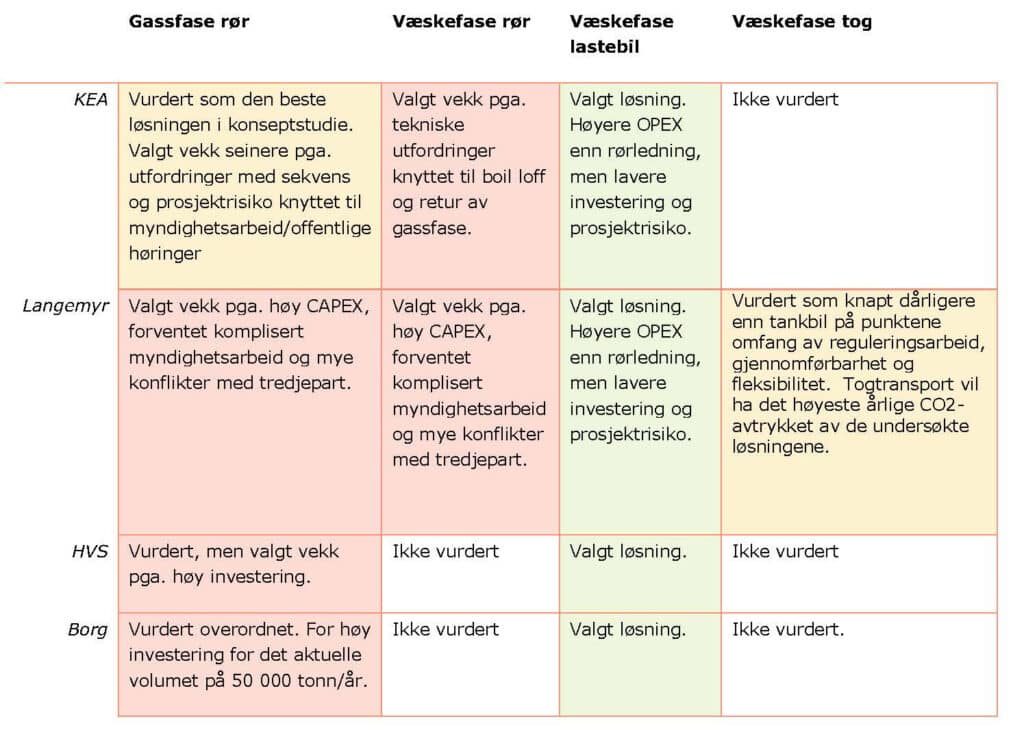
Tips: Kom tidlig i gang med vurderinger for kai-anlegg!
Consider whether it is possible to collaborate with existing players at the port by utilizing their knowledge of port operations and available space that may be available. Also, look for the possibility of using existing infrastructure at ports when establishing truck thermal needles and road systems.
Generic scalable design
The generic design for transport and intermediate storage of CO2 is based on the use of trucks. Gas-phase transport in pipelines is a good alternative and should be considered especially if the volume is high but is assumed to entail much higher project risk.
The following factors dimension the required storage volume:
- Volume flow CO2
- Size of ships
- Availability of ships in optimal size.
- Distance to permanent stock.
- Frequency of call for ships.
It is possible that there are opportunities for flexibility regarding frequency of calls and size of ships, or that intermediate storage can be arranged in several stages. For example, a smaller ship, with capacity optimized to minimize intermediate storage costs, can shuttle between the intermediate warehouse and a larger warehouse. The latter could conceivably be divided between several CCS facilities and be large enough to reduce the size and frequency of calls for ships for onward transport. This type of solution should be considered for the individual project but is not described or considered in detail here.
Generic and scalable fleet cost estimate
The following assumptions have been used to estimate the price for road goods transport of CO2:
- 31 tons are transported per car.
- It is assumed that 45 min for loading/unloading is sufficient.
- Cars travel an average of 40 km/h on the current route.
- A two-shift arrangement is established for drivers. The number of shifts must be considered in conjunction with the capacity for catch and available buffet volume at the capture facility.
Based on the above, as well as prices taken from the studies available, a unit price of 5 NOK/ton CO2/km has been applied. The same unit price is used for distances of 10 and 20 km. The difference in distance is assumed to not be large enough to have any impact on unit price. If the distances become much longer, the unit price should be adjusted upwards. Future projects must carefully review and assess the number of vehicles, the number of loading arms, the volume of buffer tanks at capture plants and shift arrangements. These are project-specific and can have a major impact on plant design and logistics operations.
In this case, dimensioning factors for the cost estimate for truck operation are volume flow, CO2 and distance between CCS plants and intermediate storage. It has been assumed that the buffer volume at the capture plant is large enough for truck transport to be carried out in two shifts.
Assessments of shift arrangements and the number of trucks in logistics operations are important from project to project. Optimized logistics will enable a reduction in installation scope and provide benefits in the form of increased resource and environmental efficiency.
The following assumptions were used in the preparation of generic and scalable tank parks:
- CO2 is offloaded to tankers with the capacity to receive 7500 m3.
- Unloading takes place at least every 4 days.
- Operating reserve is set to 1 day. 5% and 3% have been added for the upper and lower dead volumes, respectively.
- Only storage facilities, truck terminal and system for unloading to boats are considered.
- All tanks are the same size, 1000 m3. Storage requirements are rounded up to the nearest whole gross 1000 m3 tank.
The tanker port call interval and operational reserve have a major impact on the required storage volume, and these assumptions should be carefully considered. Flexibility in logistics regarding dock availability should be planned. Other players' operations in and around the dock area and other ship calls will affect this.
No tank size optimization has been undertaken with respect to the required storage volume. Tanks of 1000 m3 have been used, although in cases where the storage volume becomes high it will be more natural to store on larger tanks. The size of the storage tanks will also have a bearing on the extent of the risk area in risk assessment. A fracture in a tank (DSB) must always be assumed. Several smaller tanks may be more expensive but will be easier to handle risk-wise.
Based on the findings of the conducted studies, a cost per 1000 m3 storage tank of 35 000 000 has been estimated.
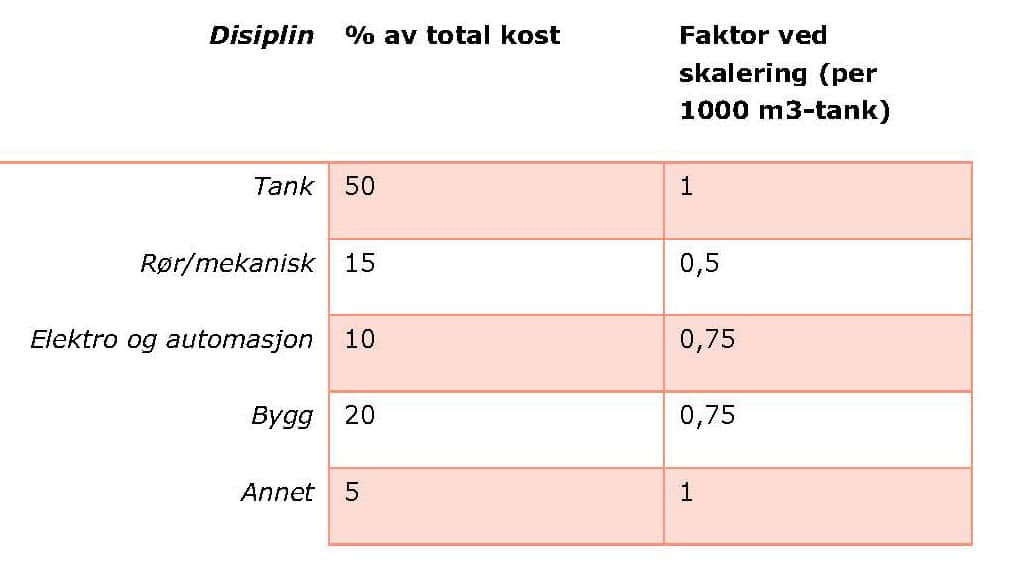
When more tanks are needed, the different disciplines have been scaled with different factors, as shown in the table (column three). These factors are determined based on qualitative assessments based on previously executed projects with a similar scope and technical composition.
In addition, a non-linear reduction in cost was modelled by increasing intermediate bearing size. For this, the same factor is used for all disciplines, shown here:
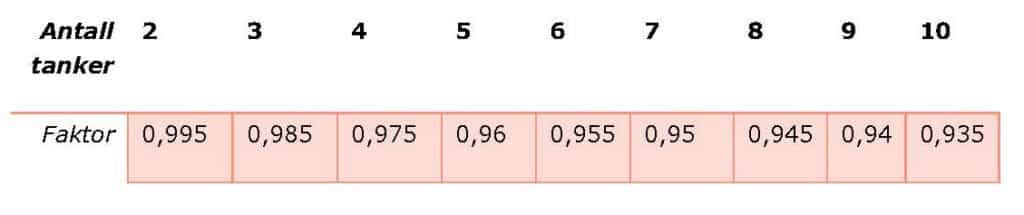
Disse faktorene er bestemt ved iterasjon og sammenligning med estimater i underlaget. Resultatene til modellen er tilpasset tidligere gjennomførte studier.
The following is included in the estimate:
- Complete tank, including insulation, fittings, valve package and instruments.
- Pipes and mechanical – pipeline for import and export, pump system and loading arms on dock.
- Power supply (from transformer) and currents. Instrument and automation.
- Necessary structural works related to the storage tank (foundations).
- Truck terminal assumed need for two unloading points.
- OPEX for tank fleet has been set at 4% of investment cost annually.
The following are not included:
- Groundworks
- Costs for facilities for maintenance cooling, gas return, VRU or similar.
- Costs for establishing docks.
- Costs related to infrastructure – high voltage power supply, water and sewerage, road.
- Costs related to property.
- Costs of liquefaction plants.
Limitations and Disclaimers
Factors such as geographical location, plant layout and ground conditions will greatly affect costs, but can hardly be considered when estimating the cost of a generic and scalable plant. Even if some of these factors are excluded from the estimate, there will be a lot of uncertainty associated with the cost. This is partly due to the following:
- Simplifications in terms of design, size, and number of tanks
- Simplifications regarding internal layout.
- Different levels of accuracy in substrates. Accuracy indicated for total investment.
- Unknown inaccuracy introduced by selected method of scaling. Qualitative assessments form the basis for factors.
The estimates prepared can be considered an indication of cost based on the studies conducted. Cost estimates in have accuracy of +- ± 20%. Some additional uncertainty is introduced regarding scaling factors in the model that has been prepared now, but accuracy in the estimates reported here is considered to have an accuracy of ± 30%. However, costs not included in these estimates will be substantial. In addition, it must be assumed that, when planning a facility, it will in several cases deviate from simplifications or assumptions made here. We can therefore not recommend using the costs estimated here for budgeting. Project-specific foundations must be used as a basis for budgeting in projects, but the model can be used as an indication in early-phase assessments.
Costs
With assumptions and methodology described, cost estimates can be prepared for several different setups. The overview below shows the range in costs of configurations as defined introductory.
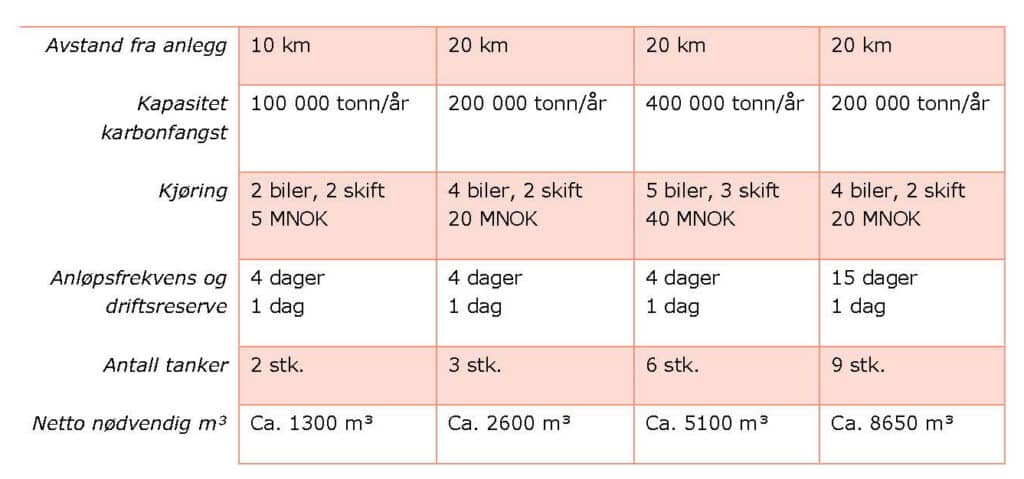
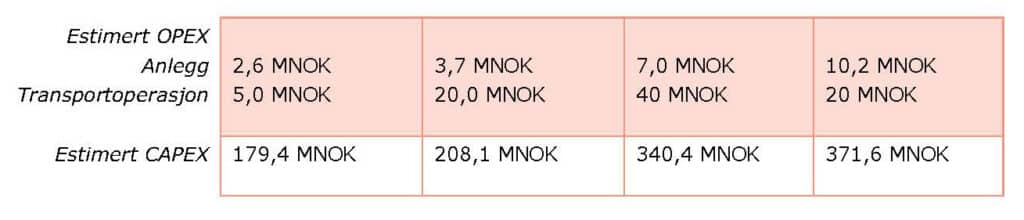
Several of the studies have assumed that tankers should arrive every four days, and that there should only be one day's operating reserve in net volume. It assumes that Northern Lights ships come to load less than full, for example 1300 m3 or 1600 m3 as in columns one and two in the table above. It is not certain at this time if this will be possible. Prices related to shipping have not been collected or estimated, but a simple sensitivity analysis has been carried out with regard to frequency of calls. Simplifications and assumptions regarding, among other things, tank size and design will have an increasing impact on larger tank parks, but the figure below gives an indication of the total cost/frequency ratio.
Tips!
Storage capacity
A larger buffer volume provides more robustness in relation to waiting time, delays, storms, and other unforeseen events at the dock. It may be worthwhile to invest in extra buffer capacity to prevent tanks from filling up and stopping truck transport.
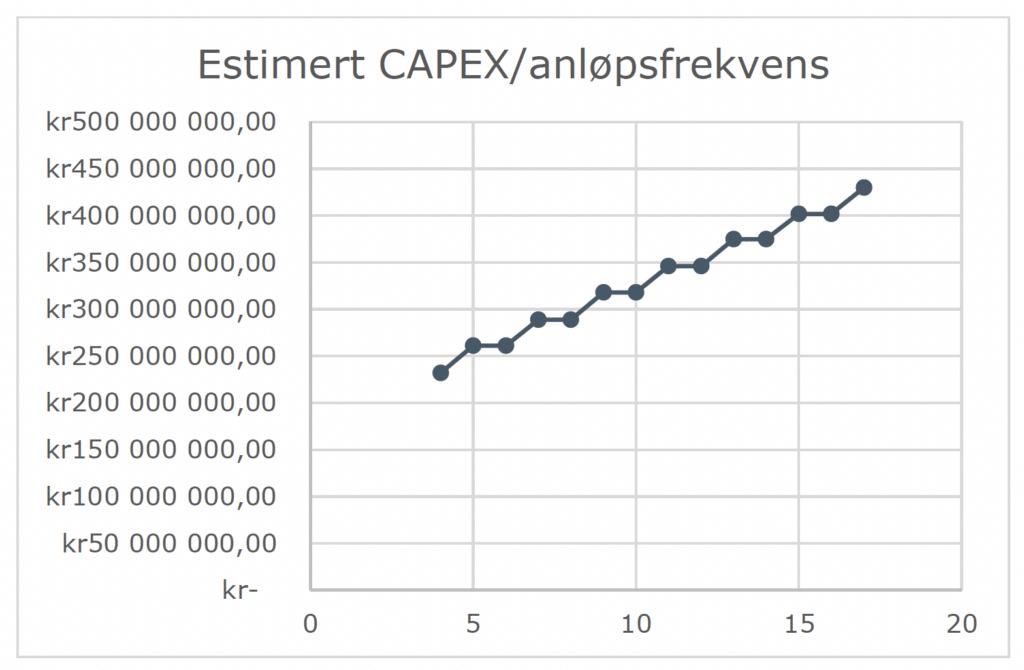
Summary
A model has been developed to make cost estimates of a generic and scalable tank park for intermediate storage of liquid CO2. The model is based on cost estimates from the substrate (the studies reviewed). The estimates can thus be considered to have a relatively high accuracy (± 30%), but they have significant limitations in the form of large cost drivers such as ground works, geographical location, property, dock facilities, infrastructure such as roads, water, sewerage and electricity supply not included. The model is also greatly simplified. The following cost estimates have been prepared:
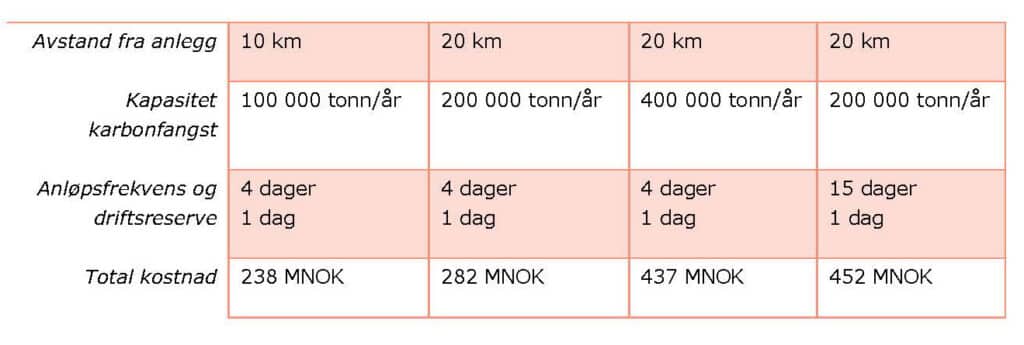